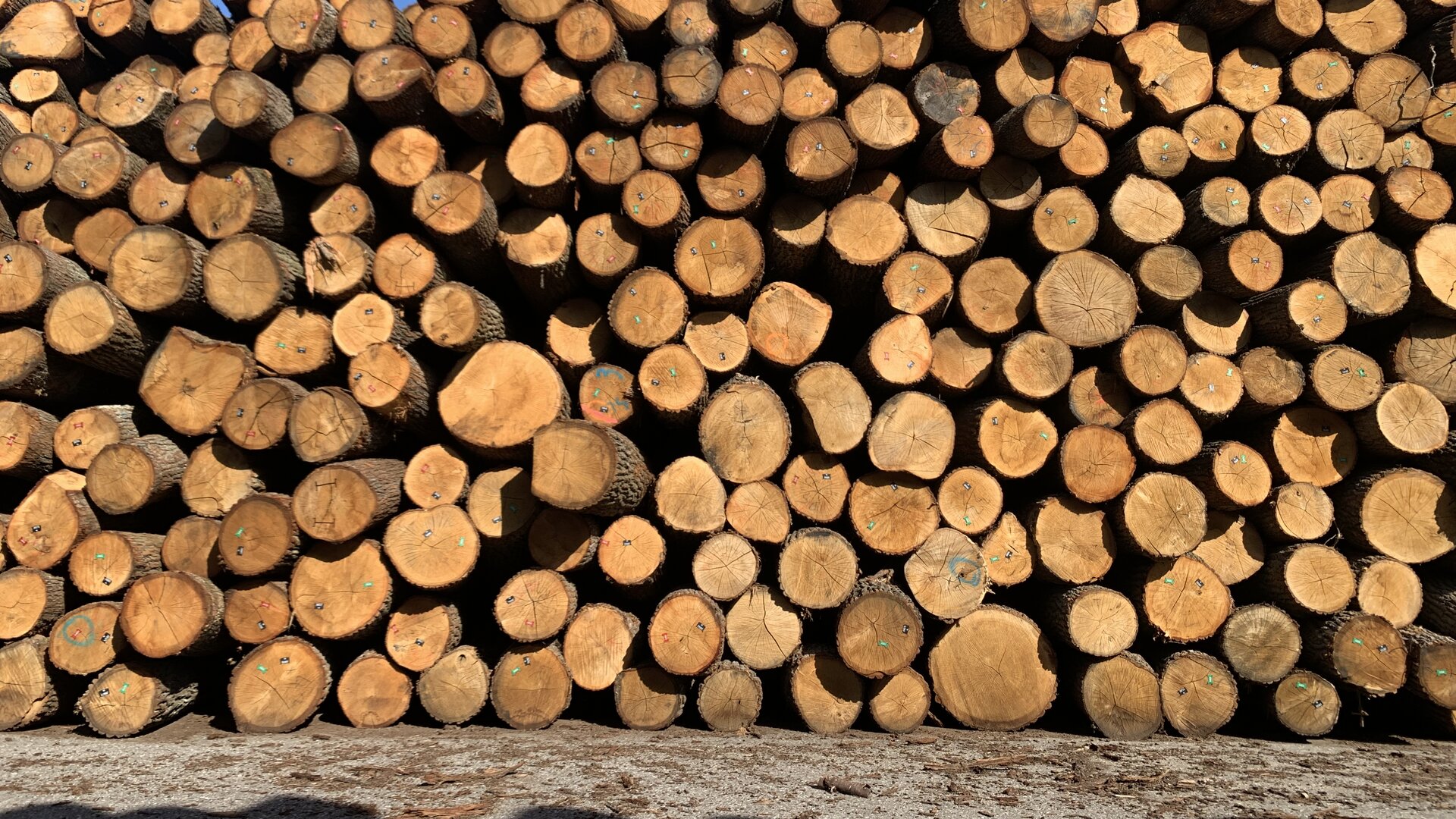
DER PROZESS
Von der Diele bis zurück in den Wald
In einem aufrichtig nachhaltig ausgerichteten Unternehmen zählt eben nicht nur das Ergebnis, sondern auch der Weg dorthin. Unser Produkt, die fertigen Diele, ist so viel mehr als nur ein Stück Holz. Viel mehr ist sie ein Konglomerat aus Handarbeit, Innovation und Natur. Hier gehen wir Schritt für Schritt zurück und erzählen die Geschichte von der Diele, die Sie kennen, bis zurück in den Wald aus dem sie stammt.

Handwerk
Die Verlegung unsere Böden bei Ihnen vor Ort obliegt den Profis, ausgebildeten Bodenlegern, die in regelmäßigen Abständen auch Produkt- und Technikschulungen bei mafi absolvieren.
Neben der Planung, Beratung und Verlegung an sich umfasst das Know-How unserer Vertiebspartner auch die Nachbehandlung vor Ort sowie die Untergrundvorbereitung.
Wertschätzung gegenüber dem Produkt
Die Lieferung unserer Dielen erfolgt in den Regionen Österreich, Deutschland und der Schweiz mit unserer eigenen LKW Flotte. Das Team BRUMIS stellt einen zuvorkommenden und flexiblen Transport sicher und achtet auf die wertvolle Ware, so wie sie es verdient.
Die übrigen Lieferungen erfolgen über Abholung oder Zustellung durch langjährige Logistikpartner zu Land, See oder Luft.
Bindeglied zwischen unseren einzelnen Fertigungsschritten ist das Team der TRANSPORTERS. Die Staplerfahrer sind unersetzlich, angefangen im Lager bis zur Kommissionierung und finalen Beladung der LKWs.

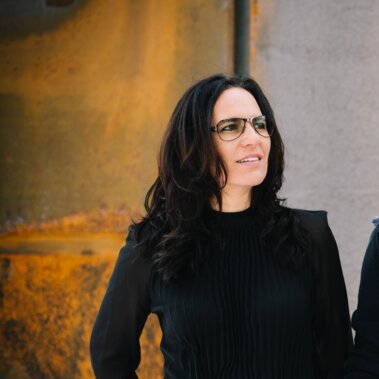
Die Beladung der LKWs erfolgt zeitnah nach Fertigungsende – ein Kernthema unserer auftragsbezogenen Fertigung. Mit einer fixen Durchlaufzeit von vier bzw. zehn Werktagen bieten wir eine schnelle, sowie planbare Lieferung. Mit unserem Ladekalender für die eigene LKW Flotte definieren wir zudem ein Jahr im Voraus die Anlieferungstage bei unseren Vertriebspartnern.
Kontrolle
Das Team TURBO VERPACKUNG ist Endkontrolle und Verpackung in Einem. Hier werden die Dielen noch einmal gesichtet und vor allem auf Vollständigkeit geprüft. Die Verpackung selbst sortiert die Dielen je nach Breite, Stärke und Typ in Pakete mit unterschiedlichen Stückzahlen.

Unsere Oberfläche
Die Öloberfläche ist das Herzstück unserer Manufaktur. Hier entsteht durch ein aufwendiges Verfahren unsere unverwechselbare, natürliche Oberfläche. In mehreren, hintereinander gesetzten Schritten werden die Dielen hier gebürstet oder geschliffen und anschließend geölt.
Der Trocknungsprozess am Ende macht dann den spürbaren Unterschied aus. Wir lassen das Leinöl langsam in die Dielen einziehen, ohne Wärmelampe oder chemische Beschleuniger. Dadurch entsteht keine Schicht an der Oberfläche, das Holz wird von Innen heraus geschützt.
Das Team TURBO arbeitet hier mit viel Erfahrung und Geduld für ein möglichst unverfälschtes Produkt.

mafi 360° Lösungen
Neben Böden fertigen wir auch hochwertige Treppen, Sockelleisten oder Wandverkleidungen.
Das Team ALLROUNDER besteht aus mehreren TischlerInnen und fertigt alle Kundenanfragen auf Maß. Auch die Bemusterung liegt in diesem Team, wo sowohl unsere Handmuster als auch größeren Musterplatten gefertigt werden.
Traditionelle Verbindung
Im Team INTERNATIONAL geht es um Präzision. Hier bekommen unsere Dielen ihre traditionelle Nut & Feder Verbindung. Wir setzen mit Überzeugung auf diese bewährte Methode und damit auch klar auf Professionisten für die Verlegung. In zwei aufeinanderfolgenden Schritten bekommen die Dielen Ihre Fräsung sowohl auf der Stirn- als auch Längsseite. Mit einer anschließenden Passprobe überprüfen wir die Qualität.





Handarbeit
Das Team TORNADO ist eines von vielen Beispielen, wo Handarbeit in unserer Manufaktur den Unterschied macht. Hier werden Äste und Risse im Material begutachtet, oft noch per Hand nachgearbeitet und harmonisiert.
Erst dann werden diese Stellen mit Harz verschlossen. So entsteht eine ganz individuelle Optik auf Basis der Natur.

Unser Dielenaufbau
An unserer Presse werden die drei Vollholzschichten miteinander verleimt. Dazu verwenden wir einen formaldehydfreien Weißleim auf Essig- und Kalkbasis.
Die Deck- als auch Rücklage kommen gemeinsam durch die Beleimungsanlage. Das Team TSUNAMI legt die Mittellage aus Weichholz im 90° Winkel auf die Rücklage. Anschließend folgt die Decklage und dann wird mit der nächsten Diele begonnen.
Ist die optimale Presshöhe erreich, kommt das Paket in unsere Presse und der Leim bindet in Ruhe ab. Auch hier setzen wir auf ausreichend Zeit und verzichten auf schnelltrocknende Industriekleber.



Handselektiert & Auftragsbezogen
Um eben diese Mittellage kümmert sich unser Team COBRA. Je nach Dielenstärke wählen wir die entsprechende Ausgangsstärke der Mittellage, die Deck- als auch Rücklage bleiben unverändert. Zur besseren Kleberhaftung wird die Oberfläche zudem noch aufgeraut.
Das Team BONANZA herrscht über unser Rohmateriallager und kümmert sich zudem um die sogenannten Tagesportionen. mafi produziert auf Auftrag und sortiert dafür für jeden Auftrag die entsprechenden Lamellen vor – Tag für Tag. Hier können dann auch spezifische Kundenwünsche berücksichtigt werden und gleichzeitig werden die zuvor sortierten Lamellen nochmals kontrolliert.










Unsere Alternative zu Tropenholz
Wir gehen den Weg möglichst viele Schritte der Herstellung in unseren eigenen Händen zu haben. Das ist ein wichtiger Qualitätsfaktor. Das Team SOS leistet in der Materialvorbereitung einen wichtigen Beitrag.
Hier werden unsere Trockenkammern mit dem entsprechenden Holz bestückt und auch die innovative, chemielose Vulcano Behandlung ist hier angesiedelt. Bei diesem Verfahren wird das Holz nur durch Wärme, Wasser und Wind getrocknet und dadurch dunkler verfärbt. So bieten wir eine heimische Alternative zur Optik von Tropenhölzern, ganz ohne Chemie und vollkommen durchgängig durch das gesamte Material.

Lamellen Kompetenz-Zentrum
In unserem vorgelagerten Standort Steindorf, nur 12km von unserem Headquarters in Schneegattern entfernt, liegt unser Lamellen Kompetenzzentrum.
Hier werden die Lamellen durch das Team TIGER durchsortiert und dabei kategorisiert. Hier entscheidet sich zum ersten Mal, ob eine Lamelle einer ruhigen oder eher lebhaften Sortierung zugewiesen wird.

Luft & Technik
Das Team BRUCE LEE bestückt die Trockenkammern und sorgt für eine schonende Trocknung der wertvollen Ware. Neben der Lufttrocknung setzen wir zusätzlich auf diese Kammertrocknung, um Verzug und Rissbildung zu vermeiden. Ein sorgsamer Umgang mit der Ressource Holz leistet einen wichtigen Beitrag zur Nachhaltigkeit.



Unser Umgang mit der Ressource Holz
Das Team SAGLA arbeitet an unseren Bandsägen und schneidet aus Rund- und Kanthölzern unsere Lamellen, die wir als Deck- als auch als Rücklage verwenden. Wir haben uns ganz gezielt dafür entschieden bereits beim Zuschnitt unsere Qualitätssicherung zu beginnen. Unser Anspruch ist auch den gesamten Baum zu verwenden. So kreieren wir ganz spezifische Designs aus Teilen des Baumes, die sonst so am Markt kaum gehandelt werden.
Das Holz selbst stammt aus nachhaltigen Forstwirtschaften Europas. Wir setzen hierfür auf mehrere kleinere Lieferanten, die wir bereits seit vielen Jahren kennen. Dank dieser kleingliedrigen Struktur konnten wir auch in schwierigen Zeiten am Markt unsere schnelle und gute Lieferfähigkeit aufrecht erhalten.
Etwaige Abschnitte und Reste verarbeitet unser Team PELLETIERER zu unseren Naturholzpellets. Damit heizen wir einerseits unser Büro und beliefern mit den Überschüssen Haushalte in der Region.




