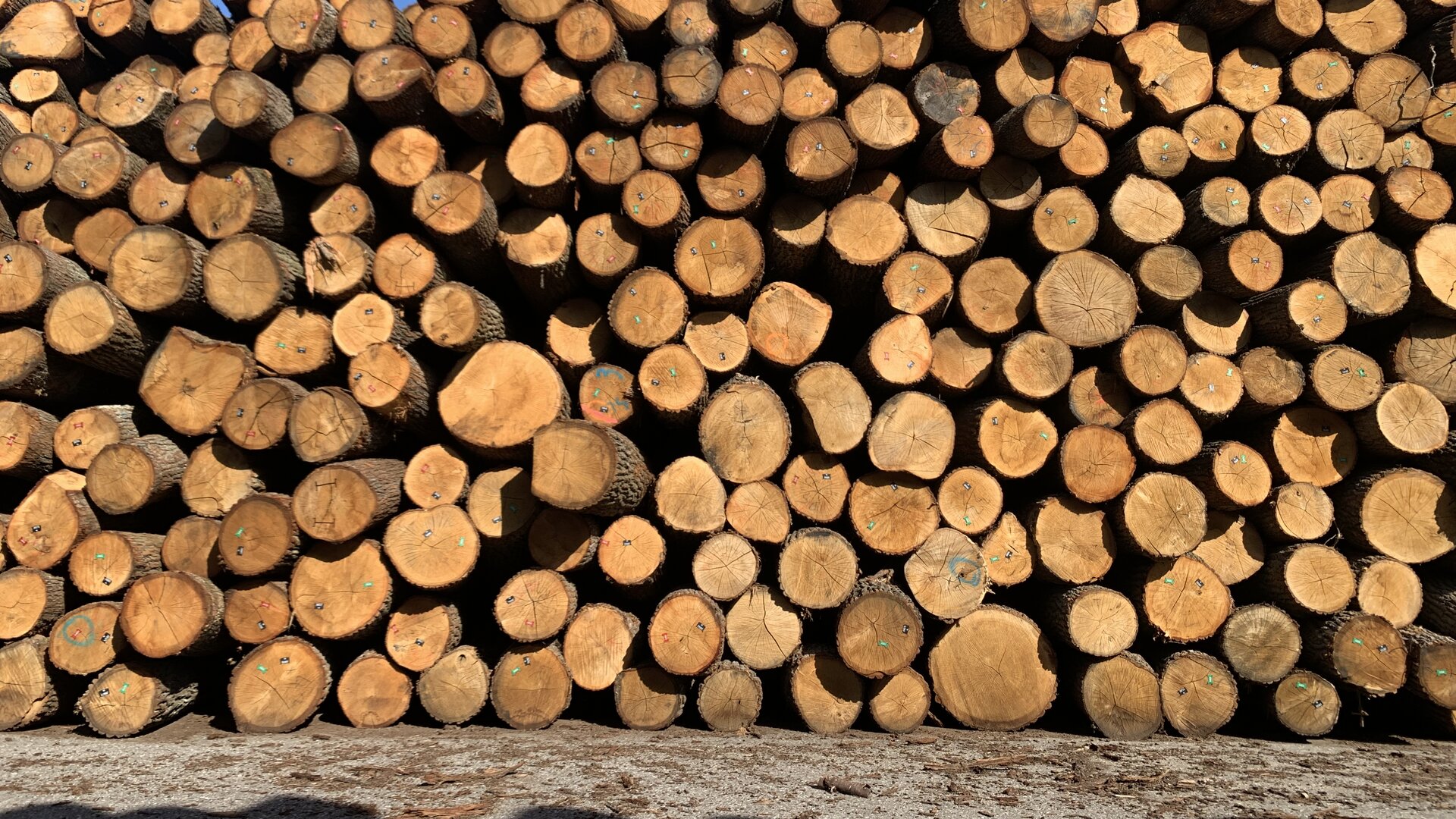
THE PROCESS
From the Plank back to the Forest
In a sincerely sustainable company, it is not just the result that counts, but also the way to get there. Our product, the finished plank, is so much more than just a piece of wood. It is much more a conglomerate of craftsmanship, innovation and nature. Here we go back step by step and tell the story of the plank you know, all the way back to the forest it came from.

Craftsmanship
The installation of our floors on your premises is the responsibility of professionals, trained installers who also participate at the mafi product and technical trainings at regular intervals.
In addition to planning, advice and installation, the expertise of our sales partners also includes on-site finishing and substrate preparation.
Appreciation of the Product
Our planks are delivered in the regions of Austria, Germany and Switzerland with our own fleet of trucks. The team BRUMIS ensures courteous and flexible transportation and takes care of the valuable goods as they deserve.
The remaining deliveries are made via collection or delivery by long-standing logistics partners by land, sea or air.
The team TRANSPORTERS is the link between our individual production steps. The forklift drivers are irreplaceable, from the warehouse to order picking and final loading of the trucks.

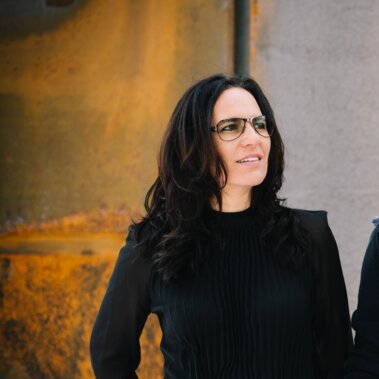
Trucks are loaded promptly after the end of production - a key aspect of our order-related production. With a fixed lead time of four or ten working days, we offer fast and predictable delivery. With our loading calendar for our own truck fleet, we also define the delivery days to our sales partners a year in advance.
Control
The team TURBO VERPACKUNG is the final inspection and packaging in one. Here, the planks are inspected once again and, above all, checked for completeness. The packaging itself sorts the planks into packages with different quantities depending on width, thickness and type.

Our Surface
The oil surface is the heart of our manufacture. This is where our unmistakable, natural surface is created using an elaborate process. In several successive steps, the planks are brushed or sanded and then oiled.
The drying process at the end then makes the noticeable difference. We allow the linseed oil to penetrate the boards slowly, without using a heat lamp or chemical accelerators. As a result, no layer forms on the surface and the wood is protected from the inside out.
The team TURBO works here with a great deal of experience and patience for a product that is as unadulterated as possible.

mafi 360° Solutions
In addition to floors, we also manufacture high-quality stairs, skirting boards and wall cladding.
The team ALLROUNDER consists of several highly skilled carpenters who produce all tailor made requests. This team is also responsible for sampling, where both our hand samples and larger sample panels are produced.
Traditional Connection
Team INTERNATIONAL is all about precision. This is where our planks get their traditional tongue & groove joint. We rely with conviction on this tried and tested method and therefore also clearly on professionals for the installation. In two successive steps, the planks are milled on both the front and long sides. We check the quality with a subsequent fitting test.





Handwork
The team TORNADO is one of many examples where manual work makes the difference in our manufactory. Here, knots and cracks in the material are examined, often reworked and harmonized by hand.
Only then are these areas sealed with resin. This creates a completely individual look based on nature.

Our Plank Structure
The three solid wood layers are glued together on our press. We use a formaldehyde-free white glue based on vinegar and chalk.
The top and back layers pass through the gluing system together. The team TSUNAMI lays the middle layer of softwood onto the back layer at a 90° angle. This is followed by the top layer and then the next plank is started.
Once the optimum pressing height has been reached, the package is placed in our press and the glue is left to set. Here, too, we take our time and do not use quick-drying industrial adhesives.



Hand-selected & made to Order
Our team COBRA takes care of the middle layer. Depending on the plank thickness, we select the appropriate initial thickness of the middle layer, leaving the top and back layers unchanged. The surface is also roughened to improve adhesive adhesion.
The team BONANZA manages our raw material warehouse and also takes care of the so-called daily portions. mafi produces to order and pre-sorts the appropriate lamellas for each order - day by day. Specific customer requests can also be taken into account here and the previously sorted lamellas are checked again at the same time.










Our Alternative to tropical Wood
We take the approach of having as many production steps as possible in our own hands. This is an important quality factor. The team SOS makes an important contribution to material preparation.
This is where our drying chambers are equipped with the appropriate wood and the innovative, chemical-free Vulcano treatment is also located here. In this process, the wood is dried using only heat, water and wind, resulting in a darker color. In this way, we offer a domestic alternative to the look of tropical woods, completely without chemicals and completely consistent throughout the material.

Lamella Competence Center
Our lamella competence center is located at our site in Steindorf, just 12 km from our headquarters in Schneegattern.
This is where the lamellas are sorted and categorized by the TIGER team. This is where the first decision is made as to whether a slat is to be assigned to a quiet or rather lively sorting.

Air & Technology
The team BRUCE LEE equips the drying chambers and ensures that the valuable goods are dried gently. In addition to air drying, we also use chamber drying to prevent warping and cracking. Careful handling of wood as a resource makes an important contribution to sustainability.



Our use of Wood as a Resource
The team SAGLA works on our band saws and cuts our lamellas from round and squared timber, which we use as top and back layers. We have deliberately decided to start our quality assurance at the cutting stage. Our aim is also to use the entire tree. In this way, we create very specific designs from parts of the tree that are otherwise rarely traded on the market.
The wood itself comes from sustainable forestry in Europe. We rely on several smaller suppliers that we have known for many years. Thanks to this small-scale structure, we have been able to maintain our fast and good delivery capacity even in difficult times on the market.
Our team PELLETIERER processes any offcuts and leftovers into our natural wood pellets. We use them to heat our office and supply households in the region.




